Simplifying Inventory Management
September 6, 2016
Having an effective inventory management system in place is vital to a practice’s growth and profitability. If you’ve ever had an inventory issue, you understand the frustration it can cause. Is your inventory count consistently off? Are your inventory reports inaccurate? Is tracking inventory an overwhelming and confusing process? Updating your inventory practices can help.
Start with an evaluation of your inventory accuracy. Why would your inventory count be off? The answer can help us determine the next course of action.
Is inventory being recorded properly?
Unrecorded inventory used can be a leading cause of inventory inaccuracy. Make sure inventory being used in the hospital and during procedures is accurately recorded. Often, inventory will be linked to a service but may not be entered until after the procedure has been completed. Have a check-and-balance system in place to assure this important step is completed.
Is received inventory recorded within an appropriate period of time?
Delaying an essential task such as recording inventory as it arrives can lead to avoidable issues. If a needed product is used before its receipt is recorded within your software, its expense to the practice may never be counted correctly, even though the cost of the item has already been paid to the vendor. This situation can throw off a number of financial reports and put you in a bind.
Are your practice management software inventory features being optimized?
The many ramifications of not utilizing the inventory features of your software correctly include inaccurate inventory reporting, stock level discrepancies and incomplete purchase ordering. In order to ensure proper use, the basics must be implemented correctly.
Making sure your items are set up correctly is imperative. Use your software’s training resources to help in this process. If using AVImark, for example, determine how you dispense the item. Set the Order Pack to the smallest received increment, such as “six-pack” in the case of Frontline. If the smallest amount you would receive would be a box of 10 cards to be sold by the card and not the individual dose, then set the Order Pack to 10 and the Package Cost to the cost for the entire box of 10.
Next, set an Order Quantity for the item. If using AVImark, this will need to be a multiple of the Order Pack. Consider the Order Point, or the amount that you will have in inventory when you want to reorder. This may change for different seasons.
If you order supplies from Covetrus and use any of the company’s software brands (AVImark, Infinity, Triple Crown, Advantage+, or DVM Manager), you may want to take advantage of Covetrus new Intelligent Inventory, which automates the delivery of inventory data to your software.
Each time an order is shipped from Covetrus, updated receipt of items information is transferred directly to the inventory module in your practice management software where it can quickly and easily be receipted, keeping inventory counts and costs accurate. As you can imagine, this saves a great deal of time, increases revenue with accurate pricing, improves inventory counts, and reduces shrinkage.
Are inventory counts being taken regularly?
To regularly monitor inventory numbers, perform a physical count of all items at least once a year, and perform a continuous “rolling or cycle count” at set intervals throughout the year. This is a continual process of validating the accuracy of inventory on a regular basis. Set dates on the calendar, or it becomes too easy to put them off and get behind. Inventory counts should be cyclic, either monthly or quarterly, as this will assist in finding discrepancies sooner.
When discrepancies are found, make sure they are recorded accurately in your practice management software. If using AVImark, make an entry in the Variance window with a clear note on why the adjustment is being made.
Are you effectively calculating stock levels and are they recalculated periodically?
Some items may require more frequent monitoring to keep the right amount on hand at different times of the year. Also, vaccine clinics, special sales, seasonal products, and increased compliance may result in higher on-hand amounts needed from time to time for specific items.
Do you have clearly defined inventory processes?
Take a look at your current processes. Are you using your practice management software to create the bulk of your purchase orders automatically? Are the inventory control activities designed to knowledgeable staff members? Are staff members encouraged to suggest ways to streamline processes or come up with new protocols that may work more efficiently? Make sure you have a clear process for damaged or return items and recording them in your software.
How is shrinkage, theft, and loss control recorded and practiced?
If physical on-hand amounts are consistently less than what your practice management software shows, several things could be the cause. One that should never be overlooked is theft. More than one staff member should be involved in inventory counts.
For example, the person counting should not be the person who tracks records. When inventory is received, two people should verify the shipment. By keeping several people involved in the inventory process, there is less chance for indiscretion.
Be sure to utilize the security features of your practice management software to restrict access to inventory changes. Too many employees with access to changing costs, on-hand, variance, etc. makes it very difficult to determine why inventory numbers are off.
Do regular inventory audits and check paper trails to verify that they match. Record all inventory losses such as breakage and damaged goods. This is especially important when considering controlled drugs. If these variances are being recorded correctly and inventory is still coming up short, theft could be a real issue.
Although it may take a few extra steps and time to avoid an inventory dilemma, in the end, the peace of mind will be rewarding. You will have confidence that your inventory control system is accurately tracking on-hand amounts and cost values, minimizing lost time tracking inventory issues and or recovering from situations that could be avoided.
About the Author
Robin Brown is director of training at AVImark. She can be reached at [email protected].
Start with an evaluation of your inventory accuracy. Why would your inventory count be off? The answer can help us determine the next course of action.
Is inventory being recorded properly?
Unrecorded inventory used can be a leading cause of inventory inaccuracy. Make sure inventory being used in the hospital and during procedures is accurately recorded. Often, inventory will be linked to a service but may not be entered until after the procedure has been completed. Have a check-and-balance system in place to assure this important step is completed.
Is received inventory recorded within an appropriate period of time?
Delaying an essential task such as recording inventory as it arrives can lead to avoidable issues. If a needed product is used before its receipt is recorded within your software, its expense to the practice may never be counted correctly, even though the cost of the item has already been paid to the vendor. This situation can throw off a number of financial reports and put you in a bind.
Are your practice management software inventory features being optimized?
The many ramifications of not utilizing the inventory features of your software correctly include inaccurate inventory reporting, stock level discrepancies and incomplete purchase ordering. In order to ensure proper use, the basics must be implemented correctly.
To regularly monitor inventory numbers, perform a physical count of all items at least once a year, and perform a continuous “rolling or cycle count” at set intervals throughout the year. |
Next, set an Order Quantity for the item. If using AVImark, this will need to be a multiple of the Order Pack. Consider the Order Point, or the amount that you will have in inventory when you want to reorder. This may change for different seasons.
If you order supplies from Covetrus and use any of the company’s software brands (AVImark, Infinity, Triple Crown, Advantage+, or DVM Manager), you may want to take advantage of Covetrus new Intelligent Inventory, which automates the delivery of inventory data to your software.
Each time an order is shipped from Covetrus, updated receipt of items information is transferred directly to the inventory module in your practice management software where it can quickly and easily be receipted, keeping inventory counts and costs accurate. As you can imagine, this saves a great deal of time, increases revenue with accurate pricing, improves inventory counts, and reduces shrinkage.
Are inventory counts being taken regularly?
To regularly monitor inventory numbers, perform a physical count of all items at least once a year, and perform a continuous “rolling or cycle count” at set intervals throughout the year. This is a continual process of validating the accuracy of inventory on a regular basis. Set dates on the calendar, or it becomes too easy to put them off and get behind. Inventory counts should be cyclic, either monthly or quarterly, as this will assist in finding discrepancies sooner.
When discrepancies are found, make sure they are recorded accurately in your practice management software. If using AVImark, make an entry in the Variance window with a clear note on why the adjustment is being made.
Are you effectively calculating stock levels and are they recalculated periodically?
Some items may require more frequent monitoring to keep the right amount on hand at different times of the year. Also, vaccine clinics, special sales, seasonal products, and increased compliance may result in higher on-hand amounts needed from time to time for specific items.
Take a look at your current processes. Are you using your practice management software to create the bulk of your purchase orders automatically? Are the inventory control activities designed to knowledgeable staff members? Are staff members encouraged to suggest ways to streamline processes or come up with new protocols that may work more efficiently? Make sure you have a clear process for damaged or return items and recording them in your software.
How is shrinkage, theft, and loss control recorded and practiced?
If physical on-hand amounts are consistently less than what your practice management software shows, several things could be the cause. One that should never be overlooked is theft. More than one staff member should be involved in inventory counts.
For example, the person counting should not be the person who tracks records. When inventory is received, two people should verify the shipment. By keeping several people involved in the inventory process, there is less chance for indiscretion.
Be sure to utilize the security features of your practice management software to restrict access to inventory changes. Too many employees with access to changing costs, on-hand, variance, etc. makes it very difficult to determine why inventory numbers are off.
Do regular inventory audits and check paper trails to verify that they match. Record all inventory losses such as breakage and damaged goods. This is especially important when considering controlled drugs. If these variances are being recorded correctly and inventory is still coming up short, theft could be a real issue.
Although it may take a few extra steps and time to avoid an inventory dilemma, in the end, the peace of mind will be rewarding. You will have confidence that your inventory control system is accurately tracking on-hand amounts and cost values, minimizing lost time tracking inventory issues and or recovering from situations that could be avoided.
About the Author
Leave a comment
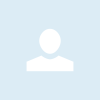
Careers
Are you looking for a place to let your talents shine? At Covetrus, we help our practitioner customers better serve their patients and take pride in providing the best customer experience possible. Search our open positions to see our available opportunities.
Newsletter
Stay current with what’s going on with Covetrus, subscribe to receive our newsletter and email communications. Subscribers will receive the latest information in practice management, sales and marketing, animal health, and more.