X-Ray Exposure: Protecting Your Patients, Clients and Staff
In today’s veterinary practice, radiography has become part of the daily routine, whether taking dental X-rays or using a full-body X-ray system, or other specialty devices such as a computed tomography and fluoroscopy. Staff members take precautions by keeping a safe distance from the X-ray equipment and wearing personal protective gear such as lead aprons, gloves, and thyroid collars. These practices are typically second nature when prepping for an exposure, but what about protecting the patient and the people in the building such as staff members, patients, and clients? Protection of the patient and the public is just as important as protecting staff members during an exposure, but how do you go about doing this?
Protecting the Patient
A veterinarian or veterinary technician can limit the exposure to a patient by ensuring they’ve had proper X-ray equipment and patient positioning training. Developing a technique chart or using one provided by the device manufacturer will help a user optimize the settings for an exposure based on the patient size and area of interest. This will limit the number of retakes and amount of radiation the patient and user are being exposed to.
Protecting the Client
Protection of your clients is equally as important to protecting your staff and patients. There is a maximum amount of radiation a member of the public can be exposed to in your clinic and you must be able to provide documentation proving you are taking the proper precautions. X-rays can easily travel through several types of wall materials and reach individuals sitting in the waiting room or patient care rooms.
Shielding plans and area surveys are the only ways to understand the radiation dose the public is exposed to in your practice. Shielding plans are a critical piece of protecting the public, as there are no mandatory guidelines that will tell you how much shielding material you need and where the material should be placed.
Shielding Plans
A shielding plan is a room design based on several parameters of your workspace. Shielding a room used for radiography is done to keep as much radiation from escaping the space as possible. To determine what kind of shielding and how much you will need to keep the public safe, you need to contact a state-qualified expert who is typically a health or medical physicist. This expert will ask for information such as specifications of your X-ray unit, where the unit is located, the composition of your walls, what the adjacent rooms are used for, and how many X-rays you take per week. They may also ask for a facility blueprint to get other specifics needed to design an accurate plan. It is very important to be precise with this information so the design matches what is occurring in your facility. The expert will then take this information and calculate what kind of shielding you need. The shielding requirements can vary and can include materials like extra drywall or lead lined floors or walls. Most states require veterinarians to have a shielding plan designed or to have a way to prove they are meeting state requirements. State violations related to missing shielding plans can result in expensive violation fees and even lead to a facility retro-fitting their existing room with shielding materials.
We’re Here to Help
If you are constructing a new facility, remodeling, or moving to a new location, it is extremely important that you work with a qualified expert to develop a shielding plan as early in the process as possible. If you are in an existing facility and have not had a shielding plan completed, you should reach out to a qualified expert to start the process.
Area surveys are also completed by a state-qualified expert, but are typically done after X-ray equipment is installed. If the survey determines that you are producing too much radiation exposure to the public, you will need to have a shielding plan designed and make adjustments according to that plan.
Covetrus is dedicated to helping keep you, your staff, patients, and clients safe during X-ray procedures and we can help you with your questions about radiation protection. Questions about shielding design, technique charts, or any other radiation protection inquiries can be emailed to Kevin.Patterson@covetrus.com
About the Author
Kevin Patterson is the Radiation Safety Officer for Covetrus, he is a state-qualified expert in many states and has an extensive background in radiation protection and health physics.
New story/blog 5
From Animal Health Solutions Q4 2018 – get images from there
OSHA Safety Training: Creating a Safer Environment for Clients, Patients, and Staff
OSHA is authorized under the law to inspect your facility to determine whether employers are complying with current regulations. OSHA enforces what is called the General Duty Clause which requires that every working person must be provided with a safe and healthful workplace. Will you be ready?
Inspections may be conducted with or without advanced notice and are often conducted based upon a current or former employee's complaint. OSHA has adopted a “worst first” system of priorities for conducting inspections that works as follows:
- Imminent Danger. These situations are given top priority. Imminent danger means that a condition is thought to exist that can be expected to cause death or serious physical harm. If an imminent danger situation exists, the Compliance Officer will ask the employer to voluntarily abate the hazard and remove endangered employees.
- Catastrophes and Fatal Accidents. OSHA’s second priority is investigating accidents that involve fatalities and/or hospitalization of five or more employees. These catastrophes must be reported to OSHA within 48 hours of the incident.
- Employee Complaints. The third priority of OSHA is the inspection of formal employee complaints of alleged violation of the OSHA Standards. The OSH Act gives each employee the right to request an OSHA inspection when the employee believes they are in imminent danger from a hazard. OSHA will maintain confidentiality when an employee requests such an inspection and will inform the employee of any action regarding their complaint.
- Programmed Inspections. These inspections are usually aimed at high hazard industries and occupations. For this reason veterinary facilities are less likely to be the target of such an inspection, although special emphasis programs or random selection may also prompt an inspection.
Inspector Credentials and Opening Conference
The actual inspection first involves the inspector presenting his/her credentials which can be verified by calling the nearest OSHA office. Remember that a Compliance Officer may never collect any violation penalty or promote the sale of any product or service. After credential presentation, the Compliance Officer will request an opening conference to explain the purpose of the visit, the scope of the inspection and the standards that apply. The employer will be given a copy of the safety and health standards that apply as well as a copy of the employee complaint, if applicable. An employer representative must accompany the Compliance Officer during the inspection. An employee representative may also accompany the Compliance Officer and may be chosen by either the Compliance Officer or the employees themselves, but may not be chosen by the employer.
The Inspection
The Compliance Officer will determine the route and duration of the inspection and will make every effort to minimize office interruptions. During the inspection the inspector may:
- Hold private conversations with employees
- Examine records
- Take photographs
- Review existing engineering controls
- Monitor employee exposure to chemicals
Closing Conference
After the inspection has concluded, a closing conference will be held and shall include the Compliance Officer, the employer and the employee representative. The Compliance Officer will discuss all alleged violations observed but no penalties will be given at this time. The employer will be given a copy of
“Employer Rights and Responsibilities”; and the Compliance Officer will discuss the contents of the booklet and answer any questions.
Citations and Penalties
A written citation and notice of proposed penalties shall be sent to the employer by certified mail. A proposed time period will be set for abatement of any violations found. The employer must post a copy
of each citation in a place visible to all employees, for at least three days or until the violation is corrected. The following violations may be cited:
- Other Than Serious Violation. This violation relates to job safety and health but is a violation unlikely to cause death or physical harm. A penalty of no more than $12, 934 for each violation may be levied.
- Serious Violation. This type of violation means that there is substantial probability that death or serious physical harm could result. A mandatory penalty of up to $12,934 per violation may be levied.
- Willful Violation. This violation occurs when the employer is aware that a hazardous condition exists, knows the condition exists and violates a standard of the OSH Act and makes no reasonable effort to correct the hazard. Penalties of up to $129,336 may be levied for each violation.
- Repeat Violation. These may incur fines of up to $129,336 each.
- Failure to Correct a Violation. This may carry a civil penalty of $12,934 for each day the violation continues beyond the abatement period.
Appeals Process
The employer may request an informal conference to discuss issues raised by the inspection citation and/or proposed penalty. The OSHA Area Director may revise citations and penalties to help avoid prolonged disputes. If the inspection was initiated by an employee complaint, as most are, the employee may request to review any decision to not issue a citation. Employees may not contest citations, amendments, penalties, or lack of penalties.
Notice of Contest
To contest a citation or proposed penalty, a written response must be sent to the OSHA Area Director within 15 working days from the date of the citation. This written response is called a “Notice of Contest”. A copy of this notice must be given to the employees authorized representative, posted in a prominent location or given individually to affected employees. After 15 days no further opportunity will be given for appeal---the citation and penalty will stand as is.
Review Procedure
The OSHA Area Director will forward the case to the Occupational Safety and Health Review Commission (OSHRC) which is an independent agency not associated with OSHA. The Commission will assign the case to an Administrative Law Judge and a hearing will be scheduled near the employer's workplace. Once the Administrative
Law Judge has rendered judgment, either the employer or employees may request an additional review by OSHRC. Any Commission ruling may be appealed to the appropriate U.S. Court of Appeals. For states that have their own occupational safety and health program, the procedures are generally similar to Federal OSHA except that the state review board or other equivalent authorities hear the cases.
Prevention Is the Key
Do any of us want to go through the exhausting procedures just described? Of course not! For this reason, it is paramount that you get your practice into compliance immediately. Begin by assigning a trusted employee to oversee/manage your OSHA compliance program. Allow them to work with a company who can provide the items needed to achieve compliance including compliance manuals, eyewash, spill kits, various safety products, personnel protective equipment, and annual required training.
Safety for Patients and Staff
The most important reason to achieve and maintain compliance is not to avoid an OSHA fine, but to create a safe and healthful working environment for your team, clients, and patients. Safety and infection control training creates an environment where better outcomes will be achieved for your patients. Such an environment will gain the respect and loyalty of your employees, who will appreciate your concern for them. In addition, you will be protecting your business from the tremendous liability and loss of reputation that may be part of an OSHA inspection that you are not prepared for.
About the Author
Karson L. Carpenter currently serves as President and CEO of Compliance Training Partners. The company works exclusively with Covetrus to provide in-office training and compliance solutions for animal health facilities.
Leave a comment
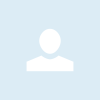
Need Regulatory Assistance
If you need help with regulatory or licensing issues, we're happy to help. We have a wide variety of resources to help you when issues arise.
Careers
Are you looking for a place to let your talents shine? At Covetrus, we help our practitioner customers better serve their patients and take pride in providing the best customer experience possible. Search our open positions to see our available opportunities.
Newsletter
Stay current with what’s going on with Covetrus, subscribe to receive our newsletter and email communications. Subscribers will receive the latest information in practice management, sales and marketing, animal health, and more.